ALEMNIS Applications
Thanks to its unmatched versatility, the ASA is the reference instrument for researchers in many fields:
- Materials Science
- Nuclear
- Bioscience
- Additive Manufacturing
- MEMS
- Electrical
- Testing
- Coatings
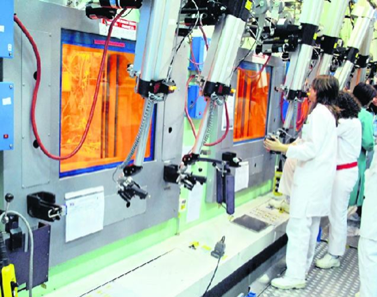
Material science
The Alemnis system has been used in thousands of studies in the field of materials science, covering all classes of materials (metals, polymers, ceramics, composites) and many different test methods (micropillar compression, tensile tests, indentation, bending of beams, mapping, fracture). toughness, fatigue and shock, impact, creep, stress relaxation, scratch tests, tribology, etc.).
It can be operated in situ in a scanning electron microscope (SEM) or other closed environment (vacuum chamber, hot nuclear chamber, etc.) or ex situ on a laboratory bench or synchrotron beamline.
In addition, the Alemnis technology can be combined with many other complementary techniques such as electron backscatter diffraction (EBSD), X-ray, tomography, Raman spectroscopy, electrical, electrochemical, atomic force microscopy (AFM), light, confocal microscopy. microscopy, to name just a few.
Some examples of specific applications of materials science:
- Compression of micropillars to investigate the toughness of hard coatingsScratch test of coatingsMEMS impact and shock testsMicropillar compression of bone pillarsCrushing tests of 3D additive fabricated structuresHardness, elastic modulus and creep of rubber O-ringsMechanical properties of hydrogel contact lenses.Properties of toothpaste additives and dental fillings.Viscoelastic recovery of automotive paint coatings.Stress-strain properties of nuclear materials in hot chamber environments.Slip deformation of titanium alloys for the aerospace sector.Contact resistance of electrical connectors under constant applied voltage.Electrochemical studies of metals in liquid cell at cathodic and passive potentials.High frequency cyclical oscillation to simulate friction conditions in metals.
Nuclear
Economic and safety concerns for current and next-generation nuclear applications call for research and development of advanced materials. At Alemnis AG we have experience in the challenging environments of nuclear research.
The Alemnis Standard Assembly (ASA) micromechanical test platform tolerates high levels of radiation, offers full flexibility for remote sample handling tasks, and can be used with light and scanning electron microscopes. The ASA was designed to test extremely small volumes of material, such as micropillars, microbeads, and particles. Since the volume of these samples is typically between 20 and 200 µm 3 , the radiation level remains favorably low.
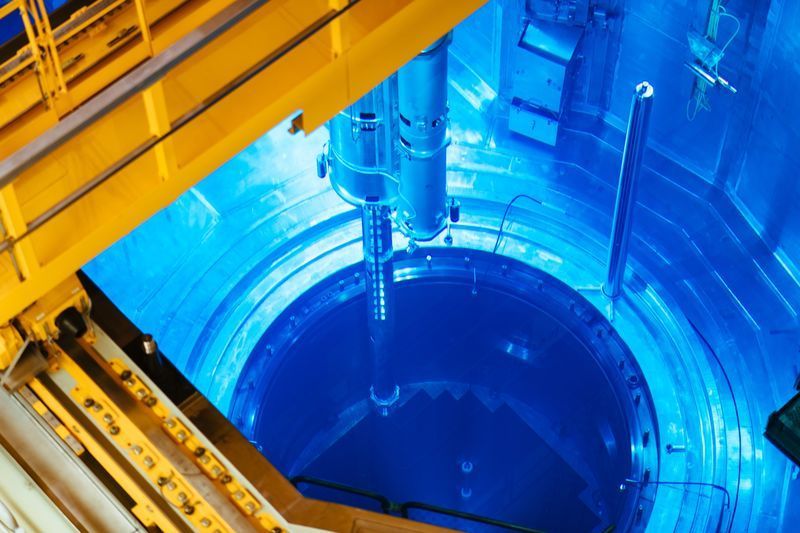
Fission
The Alemnis standard set has already been used for many studies of radioactive materials, as well as proposed replacement candidate materials for existing fission reactors.
The radiation levels of materials are reduced along with their mass. This greatly simplifies the handling of microscale samples compared to traditional mechanical test samples. Beyond the practical advantages, there are also a number of advantages from a scientific point of view.
The evaluation of the degradation of the mechanical properties of materials under irradiation is crucial for nuclear structural materials. However, macroscopic mechanical tests on ion-irradiated materials are challenging due to the shallow depth of irradiation. Micromechanical testing, on the other hand, can probe materials at length scales comparable to irradiation depths.
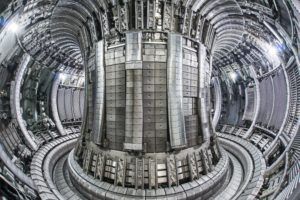
Fusion
Fusion reactors pose extreme challenges for the selection of structural materials due to severe service conditions. Viewports, for example, are complex assemblies of multiple materials including fused silica, an Inconel ferrule, and an aluminum bonding layer, where the bond is consolidated using a diffusion bonding process. The precise design parameters of such windows are the subject of continuous improvement. An important role in this effort is played by the three-dimensional finite element model (FEM).
It is important to note that these FEM simulations require stress-strain curves as input parameters. such curves are difficult to obtain from complex systems with different junctions. In the following example, dynamic spherical nanoindentation was used to map stress-strain characteristics across diffusion-bonded junctions.
A fully automated post-processing protocol can extract tensile-like properties, including yield strength, elastic strain, work hardening parameters, and elastic moduli.
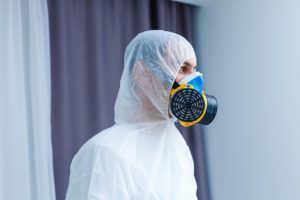
Forensic
Advances in nuclear forensics are directly related to the development of microanalytical techniques. Today, full characterization and attribution of radioactive samples is possible with just nanograms of material.
The micromechanical properties of dust particles are important variables in the description of materials of unknown provenance, and Alemnis AG is pioneering this application in collaboration with international nuclear research facilities.
Biomechanics
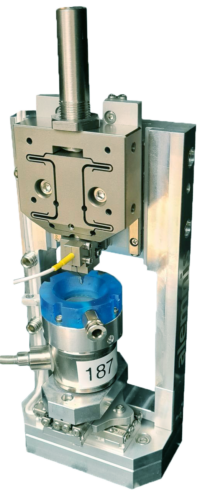
The Alemnis Standard Set (ASA) is perfectly suited for testing biomaterials in a variety of settings, both in situ and ex situ.
Examples include bone micropillars (made from FIB milling) tested within SEM, submerged biomaterials tested ex situ in a liquid cell, and analysis of biocompatible coatings for dental applications.
Liquid Cell (LIC) can be used for a wide range of experiments where the sample must be immersed in liquid. Therefore, it is normally used ex situ with the Alemnis Standard Assembly (ASA) mounted vertically and the LIC mounted on the load cell. Some examples of how the LIC can be used are:
- Immersing biomaterials in saline or body-mimicking fluid (BMF) to assess their mechanical properties when hydrated. Electrochemical tests where the indenter can be used as a current probe and the electrolyte (liquid) can be activated using an external potentiostat for corrosion studies or passivation. Studies of the mesoporous effects of the hydrogel, that is, how the mechanical properties change depending on the level of hydration. Tribological studies of interaction between the indenter and the sample when immersed in liquid. It is often used to simulate joint replacements.
additive manufacturing
The advent of additive manufacturing or 3D printing technologies has enabled the fabrication of highly complex three-dimensional geometries down to the voxel-by-voxel nanometer scale. Applications span all fields and length scales, from printed devices, biomaterials, and tools to rapid prototyping and metamaterials. However, there are still several challenges to the common use of additively manufactured components, namely material suitability, quality consistency, dimensional tolerance, and scalability limitations, to name just a few.
For many years, the development of new materials has been based on modifying the composition, such as metal alloy or polymer blend, to achieve a particular set of properties. This approach, while successful, can be time consuming, is often empirical, and only results in incremental improvement in properties. Additive manufacturing offers a very different approach: instead of finding a material that suits a specific application, the material can now be engineered for a specific use to take advantage of its unique cell structure and mechanical size effects.
Some notable characteristics of architectural cellular materials include high stiffness-to-weight ratios, negative Poisson's ratio (auxetic materials), low or negative coefficient of thermal expansion, superior electrical conductivity, heat transfer, and energy absorption. In many cases, these structures exhibit high strength and yet very low density by combining well-engineered cellular solids with nanometer-scale size effects, resulting in structures with exceptional properties.
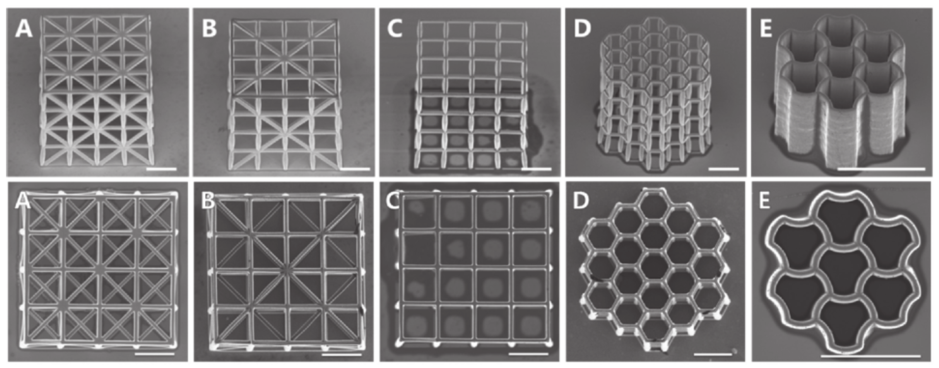
One promising route for the fabrication of cell structures is to construct a 3D polymeric template upon which a ceramic or metal coating can be deposited via atomic layer deposition (ALD) or electroless coating, for example. This produces hybrid metal/polymer or ceramic/polymer structures with superior energy absorption capabilities and optimized deformation mechanisms.
The Alemnis Standard Set (ASA) is ideal for the characterization of mechanical properties of hybrid structures by uniaxial microcompression due to its highly precise displacement control and wide displacement range (typically 40 µm, but available up to 100 µm).
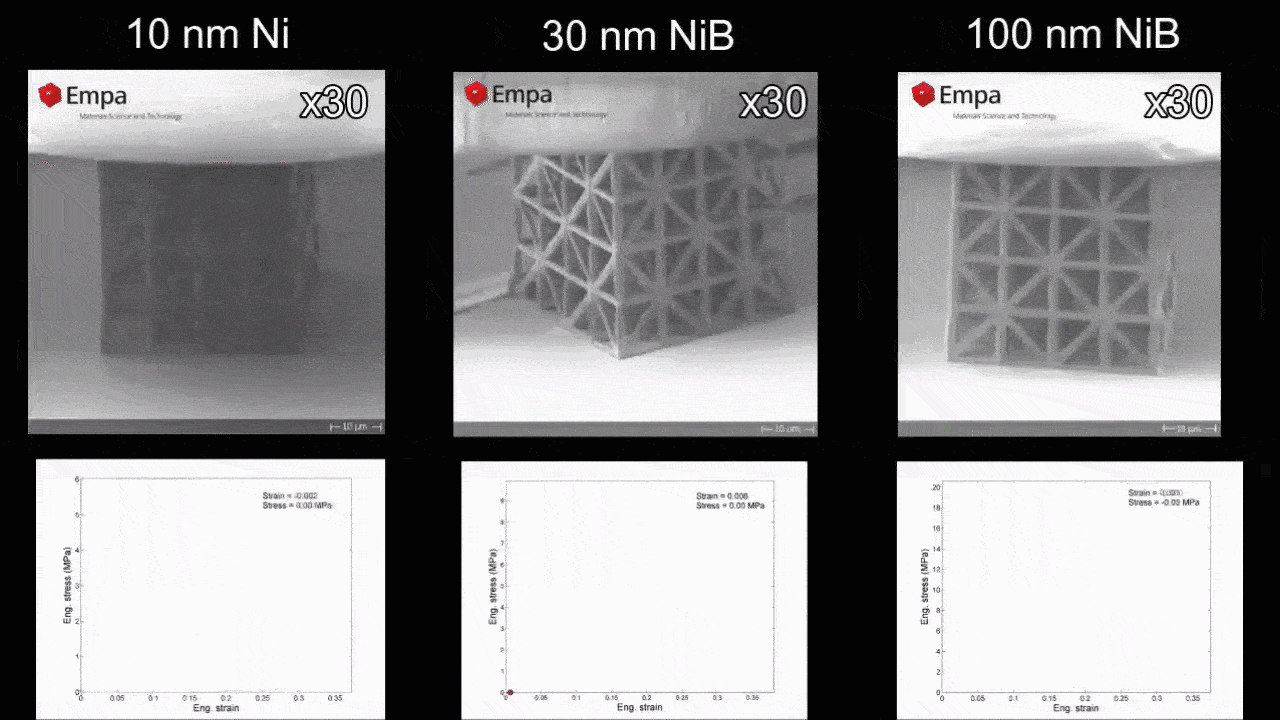
Micro Electro Mechanical Systems (MEMS)
The development of microelectromechanical systems (MEMS) has focused, in recent years, more on the manufacturing process than on issues related to reliability and the relationship with mechanical properties.
Many issues related to tribology, mechanics, surface chemistry, and materials science must be considered in the operation and fabrication of many MEMS devices. Currently, very few analytical tools are available for the accurate characterization of localized properties and specific areas of interest.
Instrumented indentation techniques provide a very powerful method for measuring the load and depth response of bulk and coated materials, but they can also be used to measure the mechanical properties of very small micromachined silicon structures. Beam structures, such as those used for accelerometers, are a good example, as they must be characterized in terms of the number of cycles to failure, the spring constant, or the energy required to bend the beam by a required amount. These localized tests must be adapted to work at various distances from the beam origin with good positioning accuracy.
The indentation method for evaluating mechanical properties at low loads and shallow depths is already well established for the characterization of thin films and bulk materials. The depth-sensing indentation method produces a load-displacement curve from which quantitative property values can be calculated using a variety of approaches. In addition, the indenter (of defined geometry) can be precisely controlled in terms of application load, depth and speed. As long as the indenter can be precisely positioned at a site of interest, the technique can be used to test the local mechanical properties of different structures, either with unique or more complicated loading cycles.
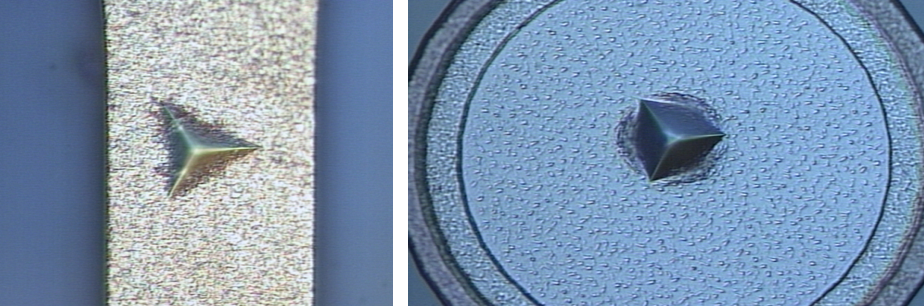
Electricity
A wide range of electrical applications are possible with the Alemnis Standard Set (ASA), ranging from electrical contact resistance measurements during material deformation to electrochemical studies using the Liquid Cell (LIC).
Liquid Cell (LIC) can be used for a wide range of experiments where the sample must be immersed in liquid. Therefore, it is normally used ex situ with the Alemnis Standard Assembly (ASA) mounted vertically and the LIC mounted on the load cell. Some examples of how the LIC can be used are:
- Immersing biomaterials in saline or body-mimicking fluid (BMF) to assess their mechanical properties when hydrated. Electrochemical tests where the indenter can be used as a current probe and the electrolyte (liquid) can be activated using an external potentiostat for corrosion studies or passivation.Studies of the mesoporous effects of the hydrogel, that is, how the mechanical properties change depending on the level of hydration.Tribological studies of interaction between the indenter and the sample when immersed in lubricant (liquid oil or grease), including experiments of tribocorrosion.
An example of a typical LIC application is the study of thin passive layers that can have significant effects on the recrystallization of nanograins in tribological contacts. The LIC is optimized to allow a metallic sample to be indented under various electrochemical conditions by applying passive or cathodic potentials in a suitable solution (for example, pH 8.5 borate solution, made from an aqueous mixture of boric acid and sodium hydroxide ). The liquid cell is converted to an electrochemical cell as shown. The sample is sandwiched between two polymer components with screws and a rubber O-ring provides a tight seal while ensuring reliable electrical contact between the sample and the working electrode.
Therefore, the design allows for reuse between samples, variation in sample geometry, and lateral movement of the indenter tip. The LIC is designed to hold approximately 1 mL of electrolyte solution.
The working electrode is made of stainless steel, 5 mm thick and 20 mm in diameter, to which a wire is welded. Four (M2) screws hold the top and bottom polymer components together. The rubber O-ring has an outer diameter of 12 mm and an inner diameter of 10 mm, thus defining the area of the sample in contact with the electrolytic solution.
The entire cell is attached to the ASA with a single screw at the base. thus defining the area of the sample in contact with the electrolytic solution.
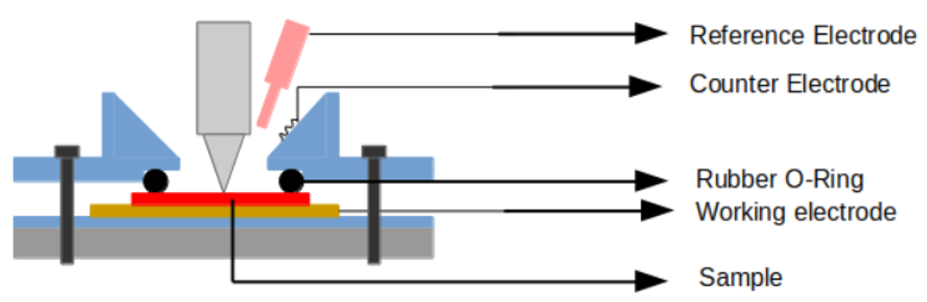
Coatings
The Alemnis Standard Assembly (ASA) has been used for a large number of studies on coatings in various forms. These can be standard coatings deposited on reference substrates, coated 3D structures manufactured by additive manufacturing, coatings used in microelectronics and MEMS, or multilayer micropillars produced by focused ion beam milling (FIM) or selective lithography processes.
Modern hard coatings, especially those used in the cutting tool industry, have become so hard in some cases that conventional nanoindentation may not be the most appropriate method to test their mechanical properties such as hardness and elastic modulus. This is due to the fact that the hardness of the coating (for example, diamond-like carbon layers with a hardness of 30-40 GPa) is not much less than that of the diamond indenter itself (̴ 70 – 120 GPa). Also, many coating companies now want to know the properties of their thin films at service temperatures, which can be on the order of 500 to 900°C. At such high temperatures, the hardness of the diamond indenter will be significantly reduced and therefore dramatically deformed, rendering point area function calibration useless for calculating mechanical properties.
ASA in situ scratch testing is also used to investigate failure mechanisms in coatings. In the scratch test, a diamond stylus is passed through the sample under a constant or progressively increasing load. Elastic and/or plastic deformation occurs at specific points along the scratch path; said critical points are observed in situ, by optical microscopy or by variations in acoustic emission and friction force.
In many cases, the scratch test has now been accepted as a versatile tool for assessing the mechanical integrity of a coated surface and has found application in many different fields of materials research. The driving forces for failure of a coating-substrate system in scratch testing are a combination of elastic-plastic indentation stresses, frictional stresses, and residual internal stresses present in the coating. The normal load at which failure occurs is called the critical load, Lc.
When scoring with progressive loading, several consecutive events of coating failure may be observed as the loading increases, the final event generally corresponding to full delamination. The critical load depends on the adhesion of the coating, but also on several other parameters; some are directly related to the test itself (intrinsic parameters) while others are related to the coating-substrate combination (extrinsic parameters).
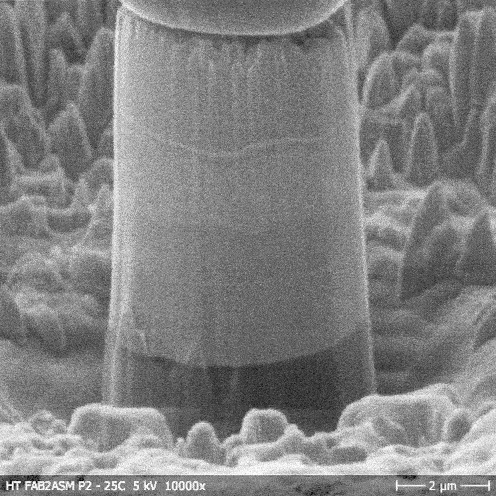
Example of micropillar compression test on a micropillar built from a multilayer pile of different coatings.
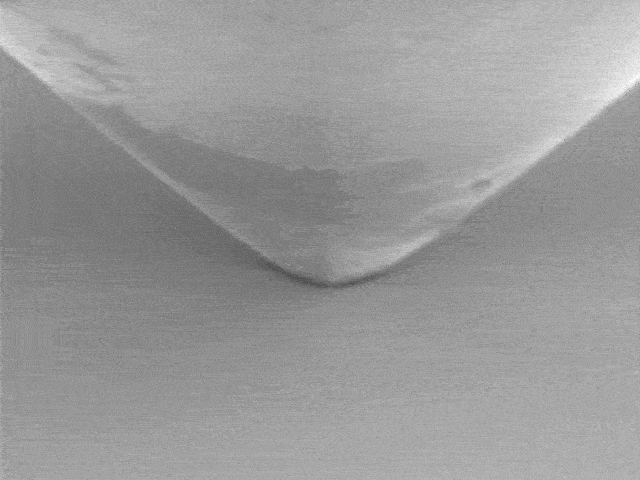
Example of scratch tests on coatings to better understand their failure mechanisms.